Centrifugal Process Pump Manufacturer
Our centrifugal process pumps are built to work efficiently in tough industrial environments. They can handle different types of liquids, including chemicals and slurries, and perform well even under high pressure and temperature. The strong materials used in these pumps help reduce the need for repairs and keep them running smoothly for longer. Designed for continuous operation, these pumps ensure your processes stay on track with minimal downtime.
With smart sealing and bearing designs, these pumps are reliable and last longer with less maintenance. They’re perfect for industries like chemicals, petrochemicals, and pharmaceuticals, offering a cost-effective way to keep your processes running smoothly and meet your specific needs. Plus, their easy-to-maintain design ensures you save both time and money in the long run. These pumps also offer flexible installation options to fit a variety of system setups.
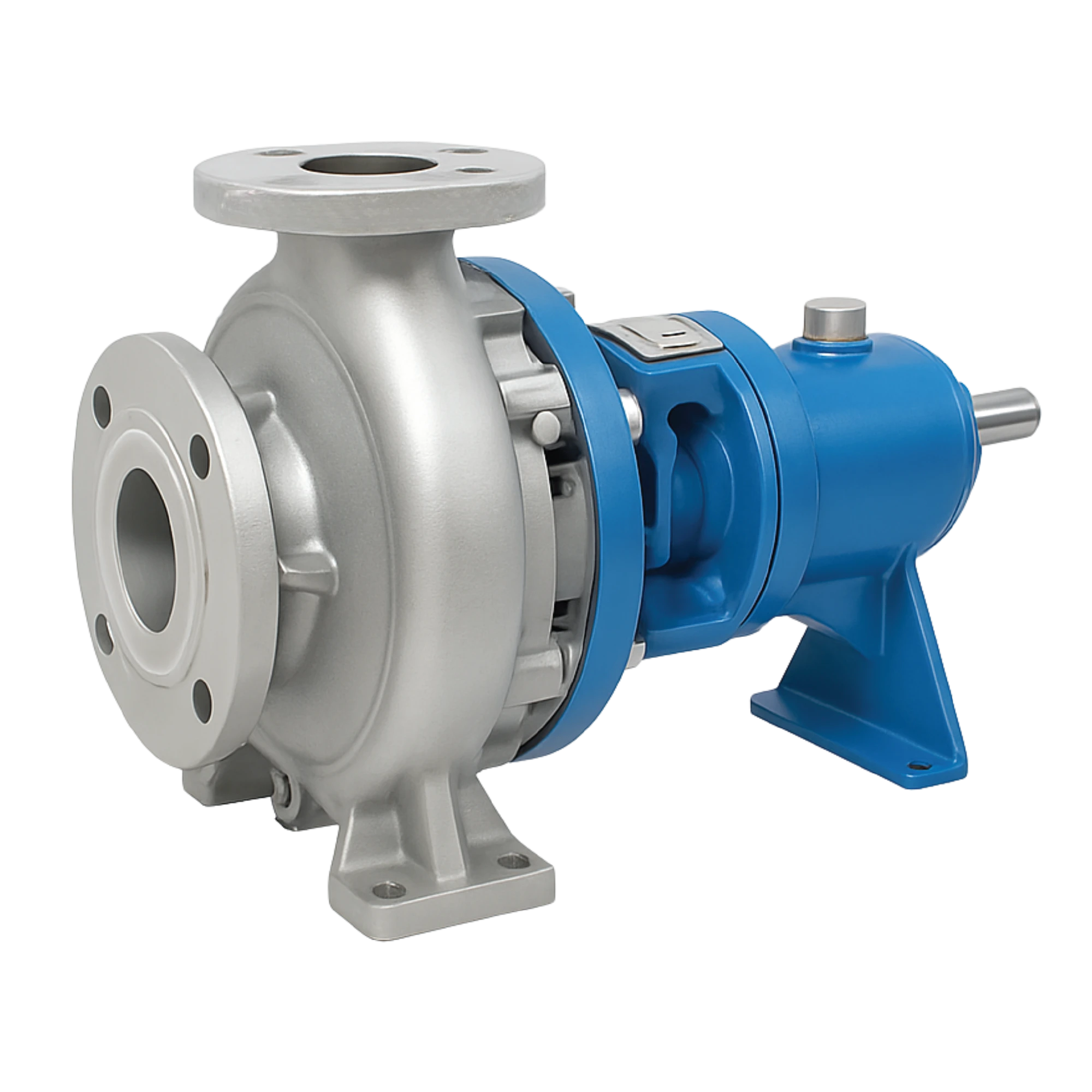
Get Reliable Centrifugal Process Pumps – Fast & Customized
Centrifugal Process Pump Cross Sectional Drawing & Design
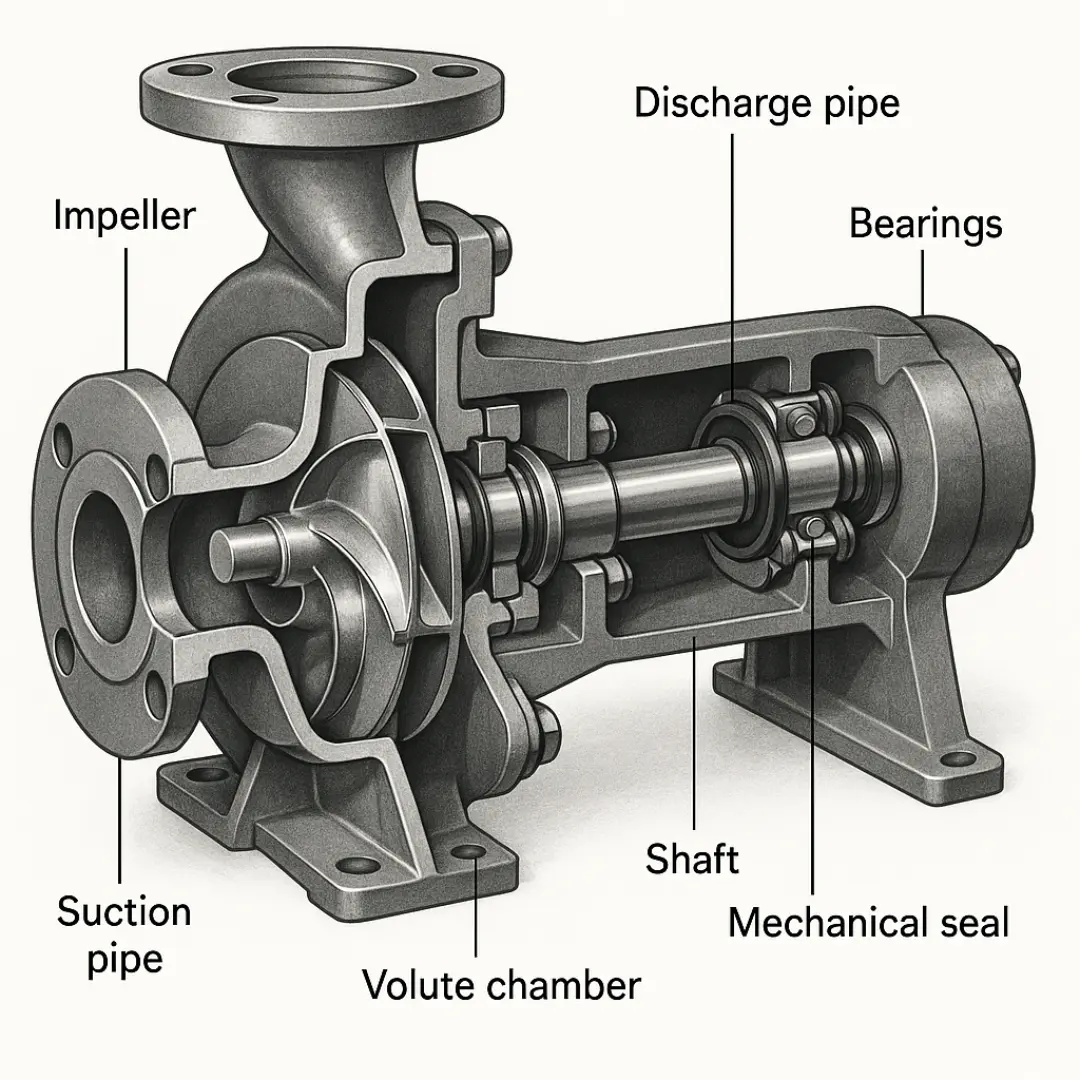
Centrifugal Process Pump Cross Sectional Drawing & Design
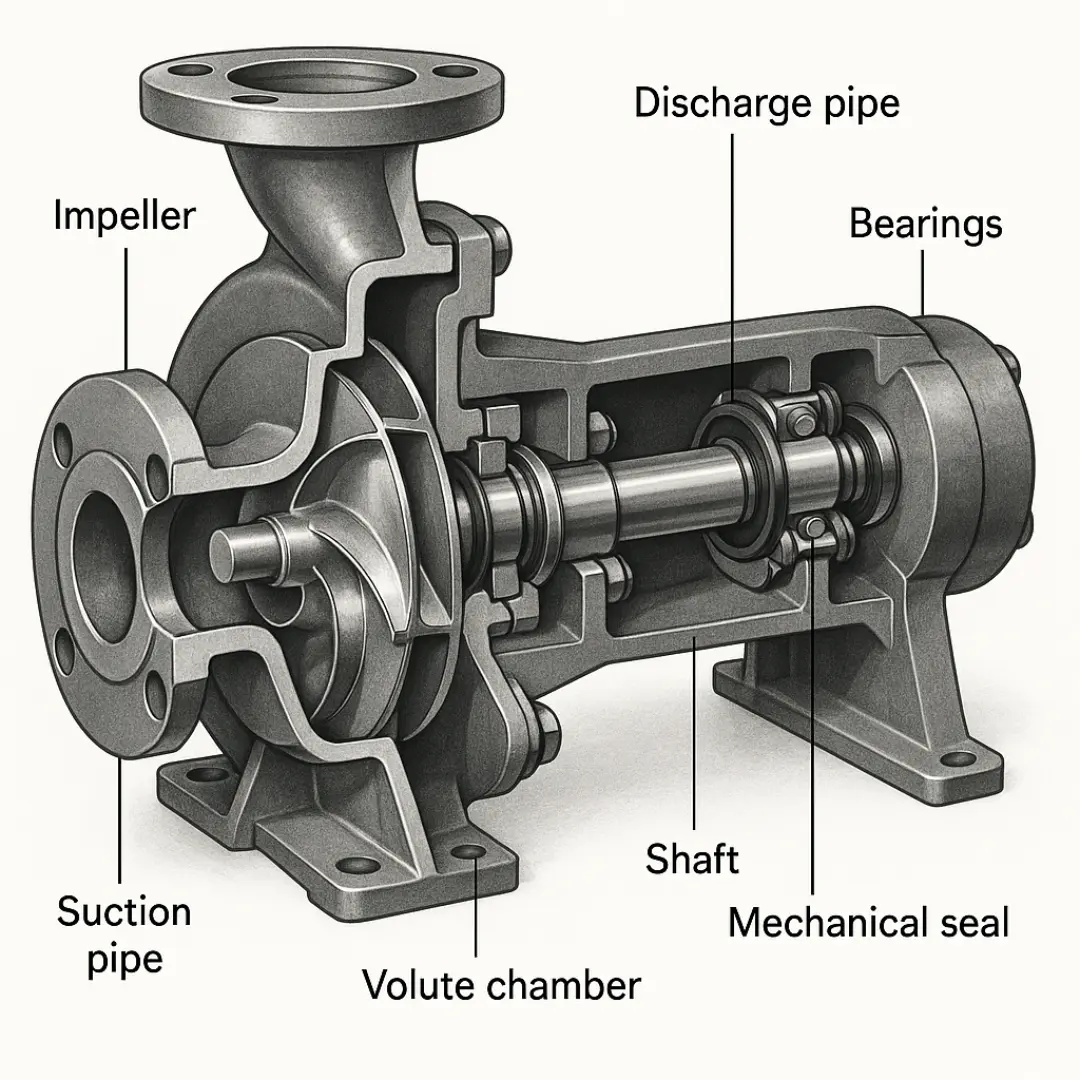
Technical Specifications of Our Industrial Centrifugal Process Pumps
Materials of Construction for Chemical Resistance
Download Our Centrifugal Process Pumps Catalogue
Applications of Centrifugal Process Pumps
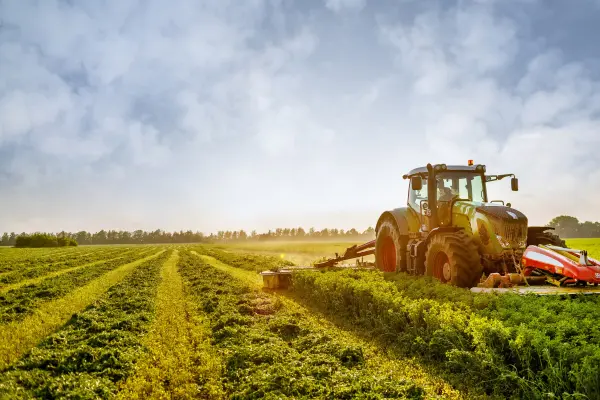
Agriculture
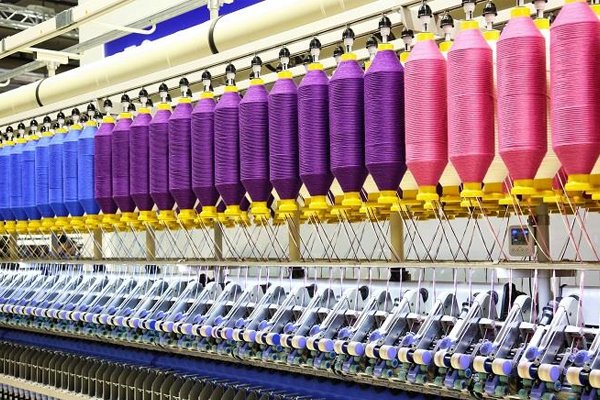
Textiles
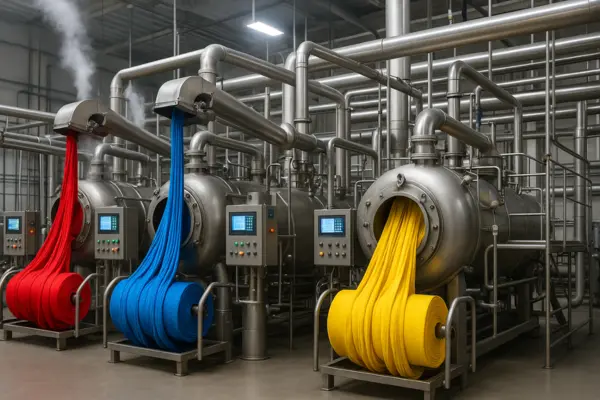
Jet Dyeing
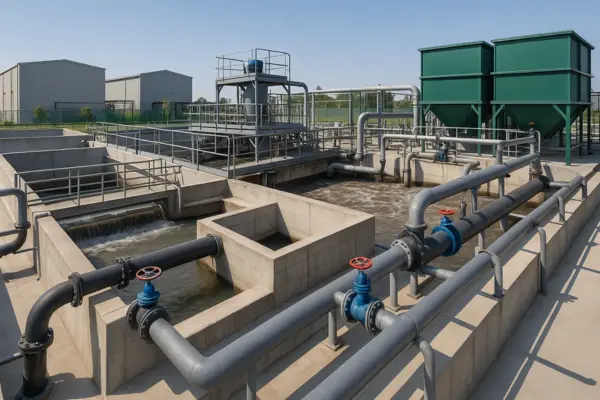
Effluent Treatment Plants

Oil Extraction
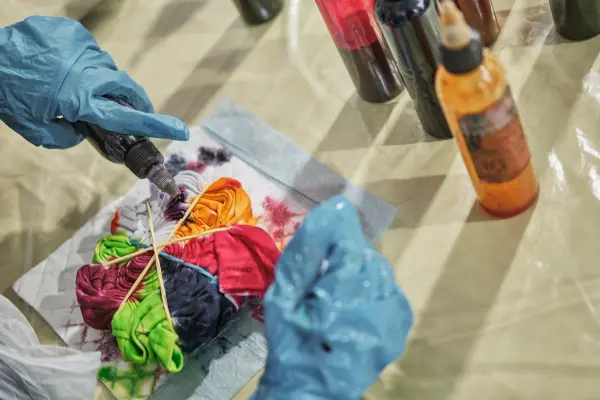
Dyes & Intermediates
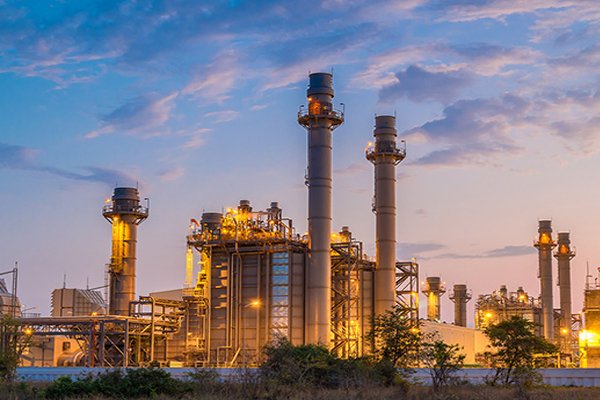
Waste Management
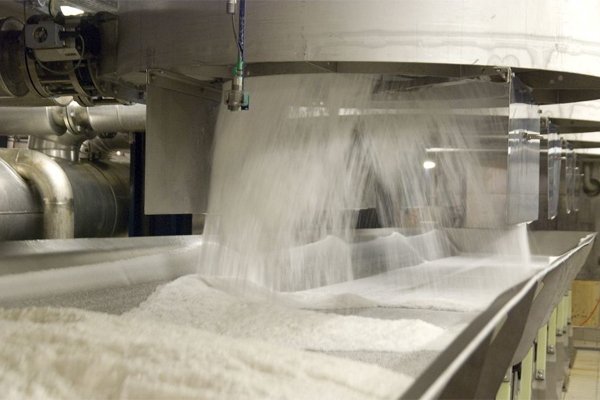
Sugar Plants
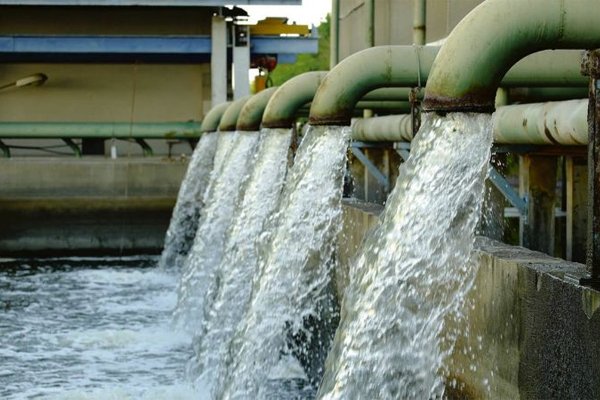
Water Supply
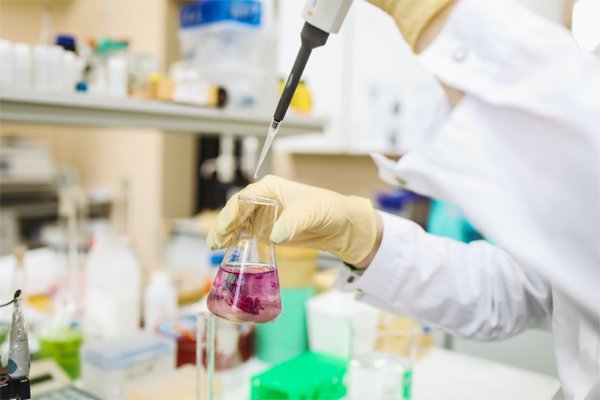
Chemical Process Industries
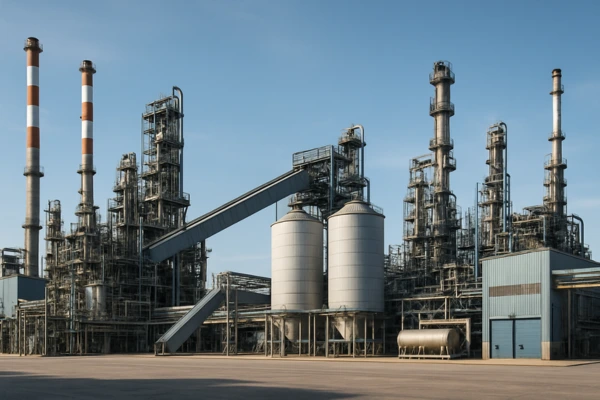
Fertilizer Plants
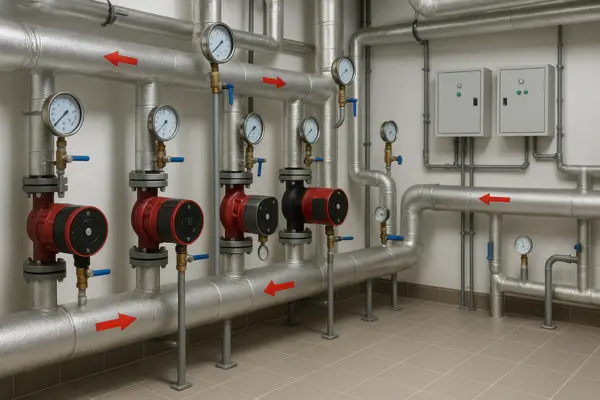
Hot Water Circulation

Cooling Towers
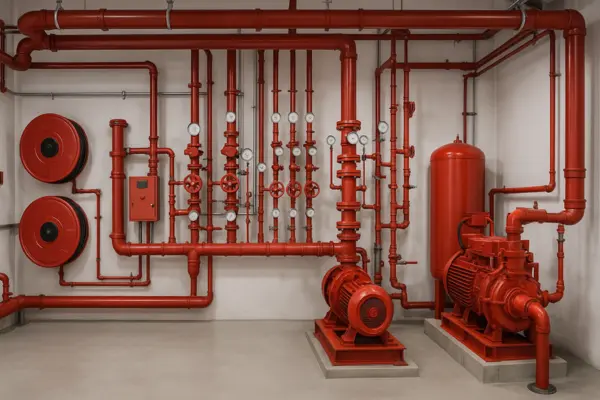
Fire Fighting Systems
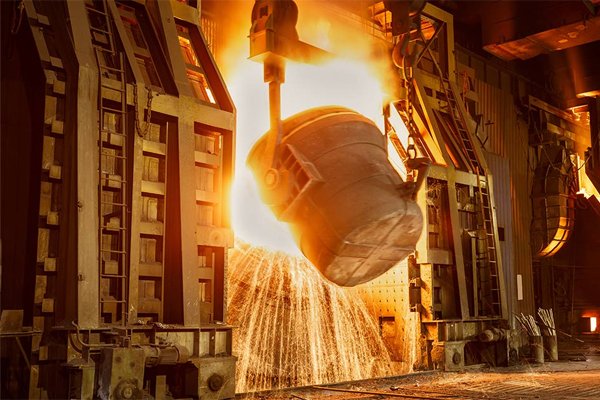
Power & Steel Industries
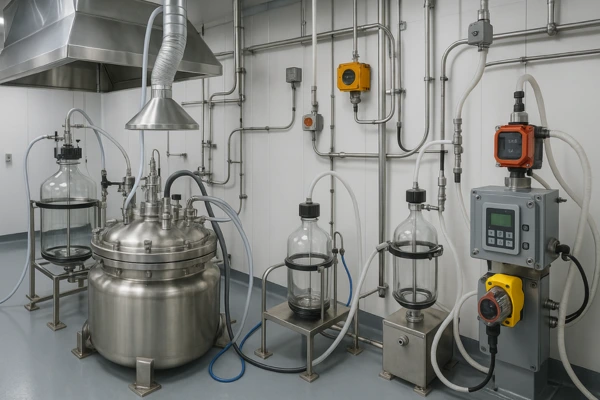
Volatile Liquid Handling
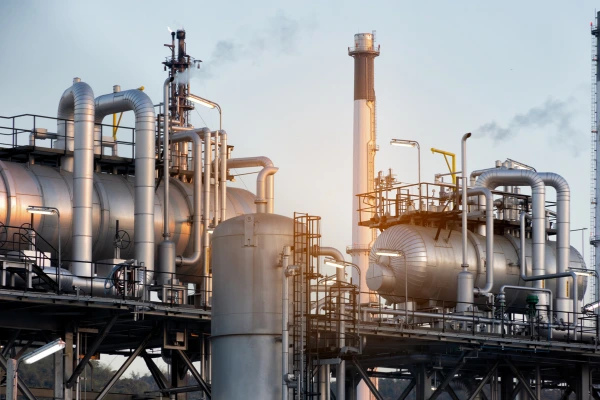
Refineries
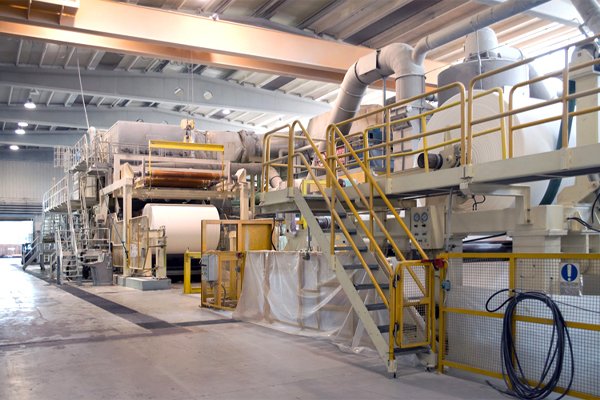
Pulp & Paper
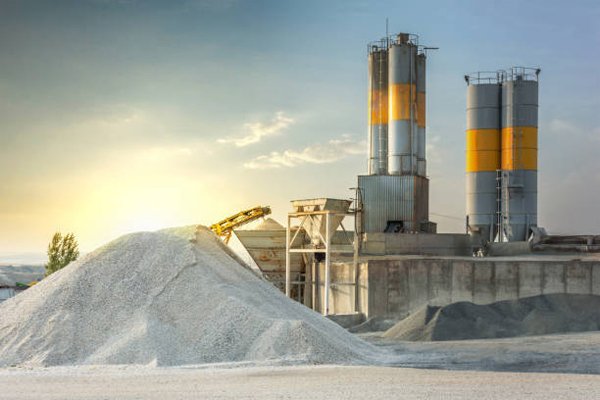
Cement Plants
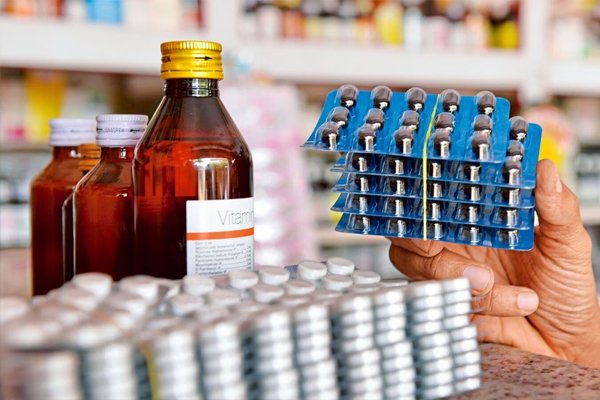
Bulk Drugs & Pharmaceuticals
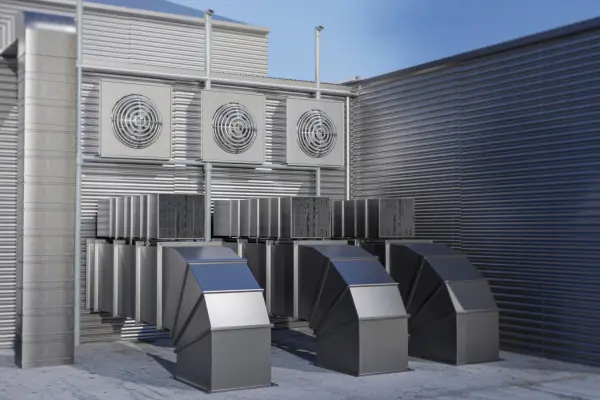
HVAC Systems
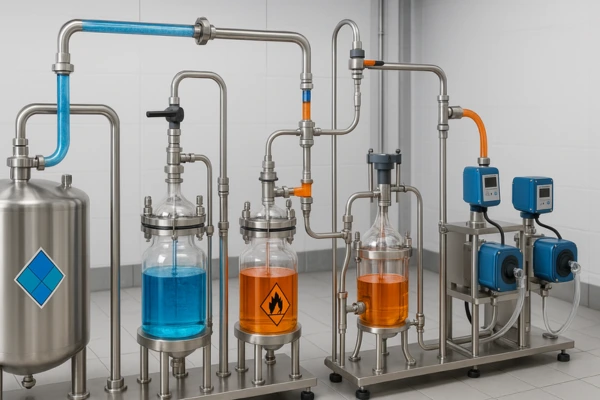
Organic & Inorganic Liquid Handling
Centrifugal Process Pump Selection Guide
Benefits of Our High-Efficiency Centrifugal Process Pumps
- Lower Operating Costs: nergy-efficient design reduces power consumption and minimizes electricity expenses.
- Minimal Downtime: Robust construction ensures continuous operation with fewer breakdowns and repairs.
- Easy Installation: Compact design and standard connections simplify installation in existing systems.
- Reduced Maintenance: Self-lubricating bearings and wear-resistant components extend service intervals.
- Versatile Applications: Handles diverse fluids from clean water to aggressive chemicals across industries.
- Long Service Life: Premium materials and precision engineering deliver years of reliable performance.
- Lower Operating Costs: nergy-efficient design reduces power consumption and minimizes electricity expenses.
- Minimal Downtime: Robust construction ensures continuous operation with fewer breakdowns and repairs.
- Easy Installation: Compact design and standard connections simplify installation in existing systems.
- Reduced Maintenance: Self-lubricating bearings and wear-resistant components extend service intervals.
- Versatile Applications: Handles diverse fluids from clean water to aggressive chemicals across industries.
- Long Service Life: Premium materials and precision engineering deliver years of reliable performance.
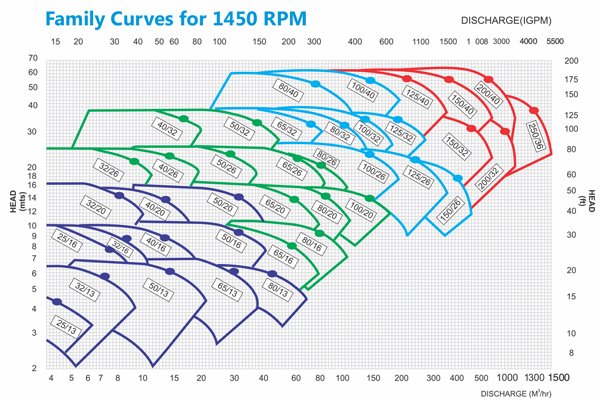
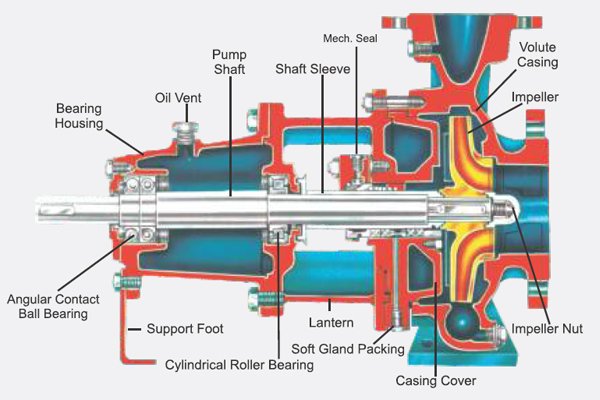
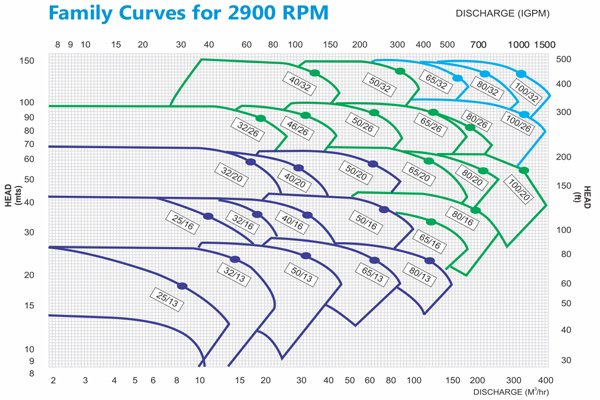
Customization Options in Industrial Centrifugal Process Pumps
Centrifugal Process Pump Installation Guidelines
1. Foundation Preparation
2. Pump-Motor Alignment
3. Suction Line Setup
4. Discharge Piping Support
5. Control Valve Installation
Customer Testimonials & Success Stories
Latest Centrifugal Process Pump Blogs & Technical Articles
Frequently Asked Questions – Centrifugal Process Pumps
Q1: What is the price of centrifugal process pumps in India?
MRP Pumps offers competitive pricing for centrifugal process pumps. Contact us for detailed quotations based on your specifications.
Q2: Which is the best centrifugal process pump manufacturer in Ahmedabad?
MRP Pumps is a leading centrifugal process pump manufacturer in Ahmedabad with 15+ years of experience and proven industry expertise.
Q3: How to select the right centrifugal process pump for chemical applications?
Consider flow rate, head pressure, fluid properties, temperature, and material compatibility. Our experts provide free consultations.
Q4: What is the difference between centrifugal and positive displacement pumps?
Centrifugal pumps use rotating impellers for continuous flow, while positive displacement pumps use chambers for precise volume transfer.
Q5: How long do industrial centrifugal process pumps last?
MRP centrifugal process pumps typically last 10-15 years with proper maintenance in industrial chemical processing applications.
Q6: What maintenance is required for centrifugal process pumps?
Regular bearing lubrication, seal inspection, impeller cleaning, and alignment checks ensure optimal pump performance and longevity.
Q7: Can centrifugal process pumps handle corrosive chemicals?
Yes, MRP pumps use corrosion-resistant materials like stainless steel and specialized alloys for aggressive chemical applications.